First-ever ‘Space Weld’ could pave way for lunar living

John E. Kaye
- Published
- Home, News, Technology
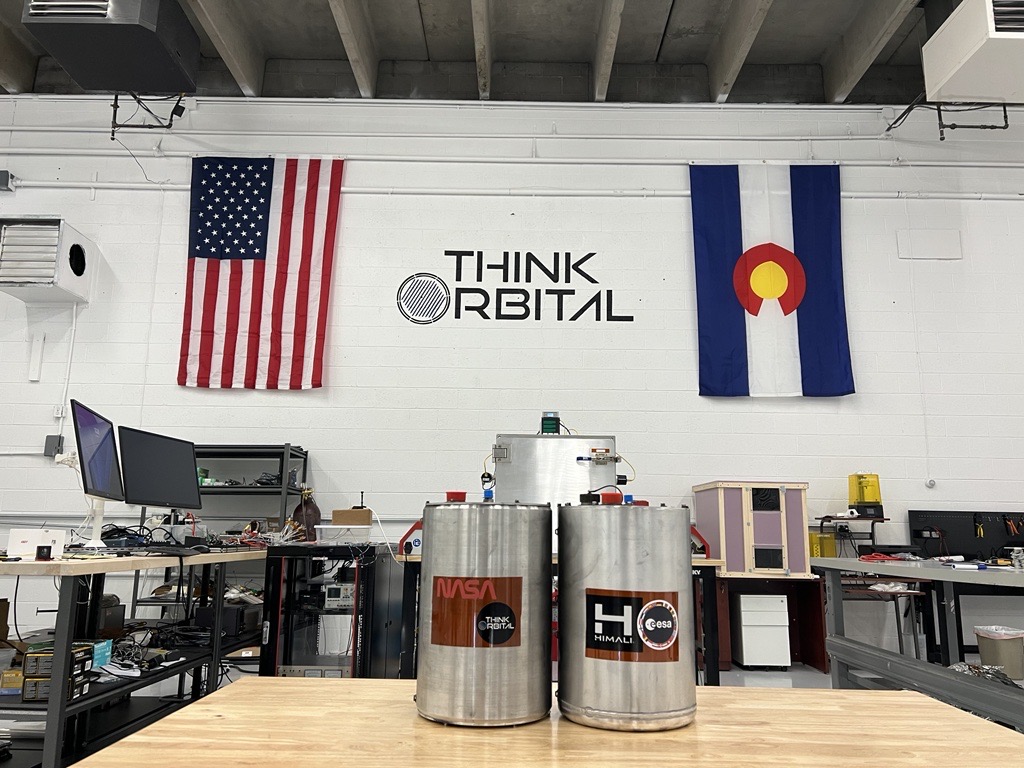
It was one small step for man but, conceivably, a giant leap for mankind
NASA’s hopes of building homes on the moon inched closer to reality last week after the first-ever robotic weld was carried out in space.
An autonomous welding machine successfully fused a series of aluminium plates together in a “historic” test that could pave the way for large-scale lunar construction projects.
The machine uses electron beam welding (EBW) technology to precisely melt and join metals in zero gravity.
It can be deployed in environments with extreme temperature changes and in conditions well below normal atmospheric pressures, making it ideal for use in the vacuum of space.
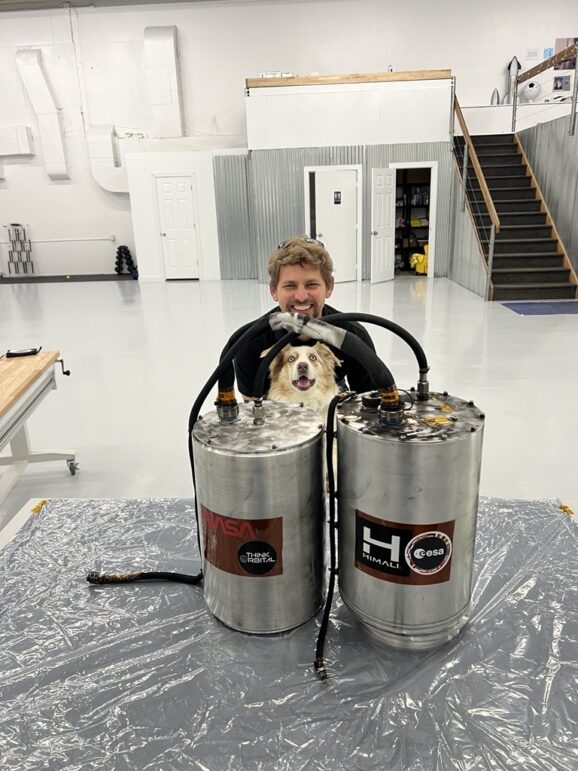
The US firm behind the technology, ThinkOrbital, said the In-Space Servicing, Assembly and Manufacturing (ISAM) tests marked a “significant leap forward in space innovation”.
It is now planning to test other parts of its welding system, which include an autonomous robotic arm with X-ray capabilities, later in the year.
If those experiments are also successful, the technology will be used to repair satellites and spacecraft in orbit, reducing the need for expensive manned missions.
But the same welding system could also be used to fabricate space station modules and other metal habitats to support human life – a key NASA objective.
In 2022, the American space agency awarded US construction technology company ICON $60 million to build a home on the moon by 2040.
ICON plans to take a giant 3D printer to the moon and use lunar concrete made of rocks, mineral fragments and dust to layer the structure on the surface.
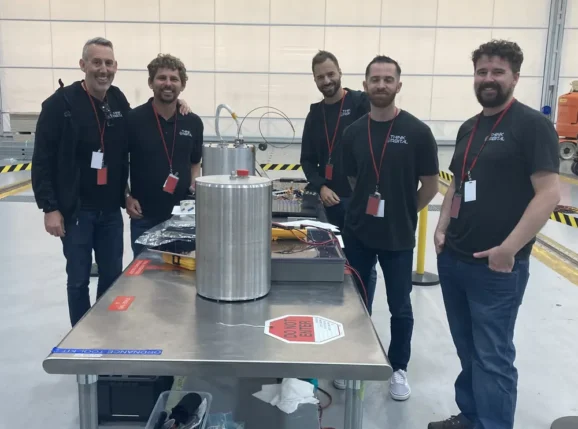
A spokesman for ThinkOrbital said: “We are thrilled to announce that we’ve achieved the majority of our Flight-1 objectives, marking a significant leap forward in space innovation.
“Our journey has been nothing short of extraordinary, from the groundbreaking first-ever autonomous in-space weld to the historic return of flown-in-space Electron-beam welder samples.
“These samples will be meticulously analyzed by NASA and the European Space Agency, paving the way for groundbreaking discoveries.”
ThinkOrbital’s welding system was sent to space on board the SpaceX Falcon 9 on May 6.
The metal test plates it welded were returned to earth on the Falcon’s booster and the strength and accuracy of the welds are currently being examined by NASA and the European Space Agency.
ThinkOrbital was among the companies NASA chose last year for Space Act Agreements, which aim to advance commercial space capabilities.
It said: “Throughout this milestone-filled journey, we have designed and built the world’s first autonomous in-space welding system, conducted and passed rigorous vibration, shock, and thermal testing, garnered FAA and FCC flight authorization, and successfully launched and landed on Falcon 9 on May 6, 2024.
“This is just the beginning of our continued commitment to pushing the boundaries of possibility in space exploration.”
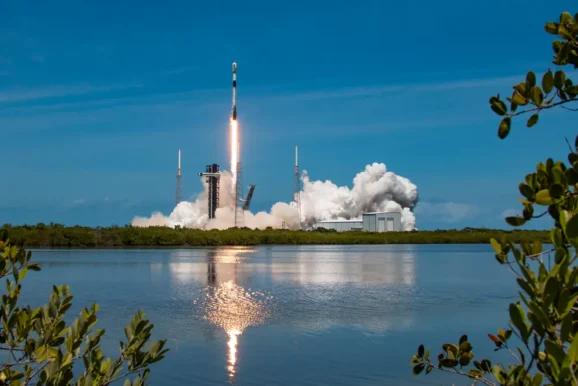
Video – courtesy of ThinkOrbital
Images © ThinkOrbital
RECENT ARTICLES
-
Scientists are racing to protect sea coral with robots and AI as heatwaves devastate reefs
-
Game, set...wax. Billie Jean King statue unveiled in New York
-
Vegas on a losing streak as visitors drop 11%
-
The European launches new Digital Content Exchange Network
-
Munich unveils new hydrogen lab as Europe steps up green energy race
-
Dubai Humanitarian launches film highlighting $48m global aid effort
-
Inside MINISO’s new giant Amsterdam store aimed at Europe’s Gen Z shoppers
-
Global demand drives record enrolment at Mohamed bin Zayed AI University
-
Tech boss’ dream private island on sale for £3m complete with fortress, helipad and...nightclub
-
The European in the Amazon as COP30 drives global climate decisions
-
The European takes its place at the table as G20 heads to Johannesburg
-
Specsavers to invest £5M in UK facility expansion to boost lens production
-
Abu Dhabi asserts leadership in regional property market as IREIS 2025 prepares to welcome 2,000 investors
-
Hulk Hogan: the world’s first athlete to become a global franchise
-
Pop star: Mumm sends champagne to space
-
Europeans are warming to EVs – and to Chinese brands
-
Sagrada Familia tops global rankings as Tripadvisor reveals world’s best travel experiences for 2025
-
Up, up and bouquet! Giant flower balloon lifts Medellin’s festival spirit
-
Europe and UK lag behind in global giving as low-income nations lead
-
Chinese carmaker GAC to launch electric cars in Britain
-
British firm Skyral to help Mongolia tackle pollution with AI traffic modelling
-
Seaweed and wind turbines: the unlikely climate double act making waves in the North Sea
-
Bahrain joins global subsea network as stc lands 2Africa Pearls cable
-
UAE emerges as global contender in digital infrastructure
-
Out now: Inside the Summer 2025 edition of The European